As the weeks progress we are getting closer and closer to having a complete competition robot ready and on the field during competition. Starting off the week with lots of field and drive testing while each team improves their wiring and prototypes. While the drive base team continues to work on wiring, each of the mechanism teams iterate their final designs for assembly and mounting on the competition robot.
Drive Base & Climber
The drive base team has tested and cleaned up the wiring of the robot, the camcorder also replaced. A new top layer for the belly pan was made in CAD then laser cut to attach to the robot. While the camcorder was replaced the drive base team started the limelight, RSL, and radio mount. The bumper latches were also attached to the drivebase. After some testing the drive base team had a successful drive test with the competition robot, YIPPEE!
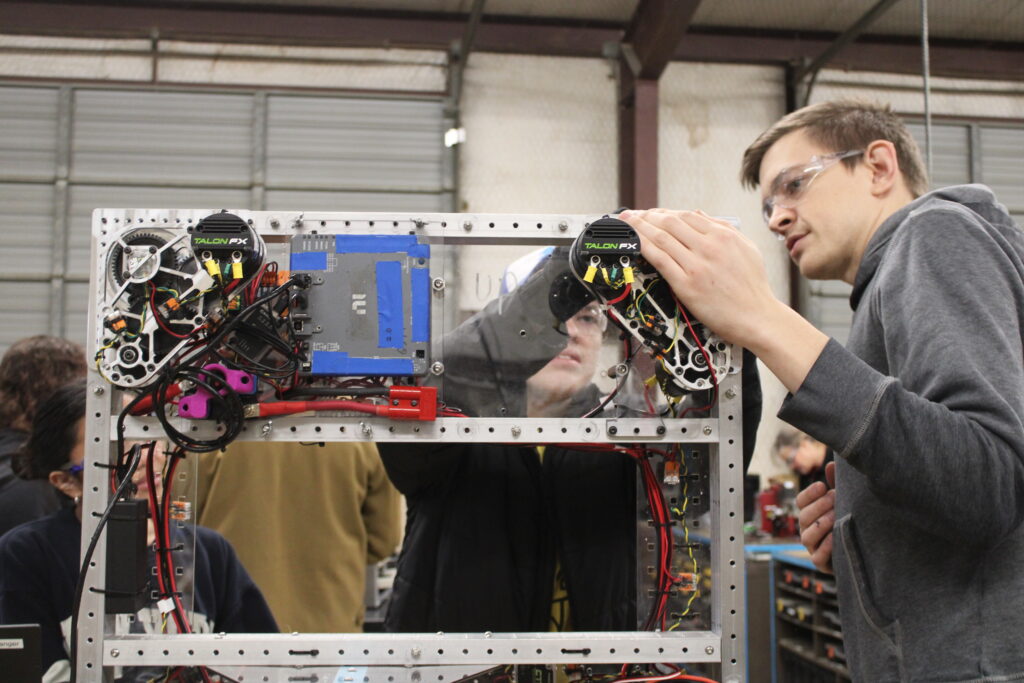
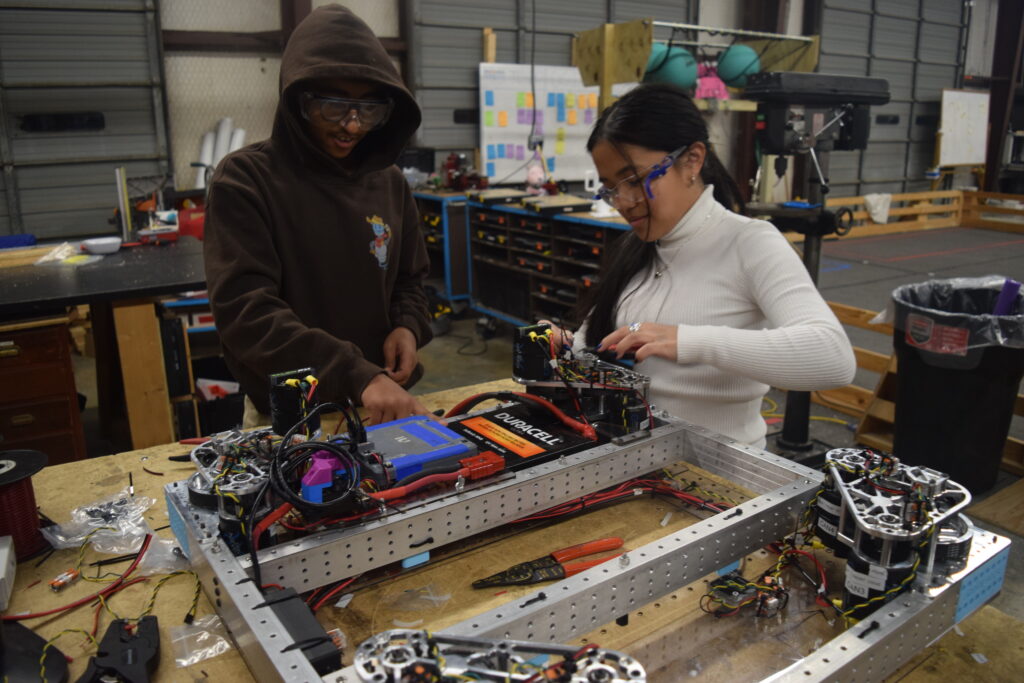
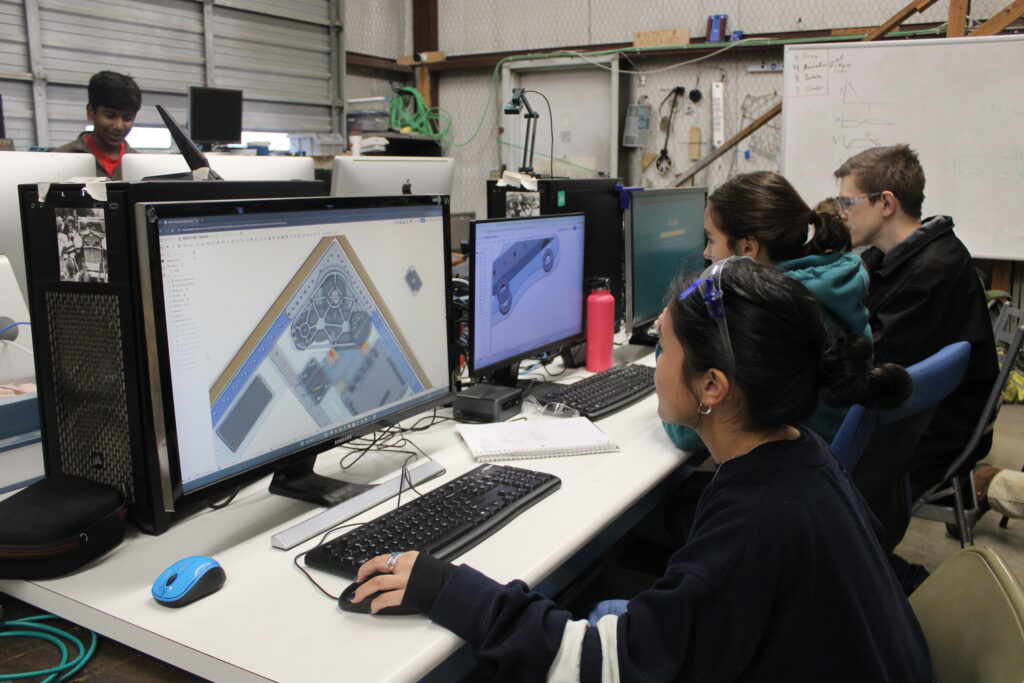
Ascender
The elevator has already been successfully mounted on the competition robot, marking great progress. However, the team hasn’t stopped there—several thoughtful refinements have been made. The rollers were carefully repositioned to the top, and a custom extension was added to more effectively catch the game piece as it exits the intake, improving both speed and accuracy. To power the elevator, the team has opted for the Kraken, which is paired with a time-of-flight sensor for pinpoint precision in detecting when a game piece has been successfully captured. As an added bonus, the elevator system has also been wired into the drive base, allowing the Krakens to run efficiently and provide full support for the entire assembly.
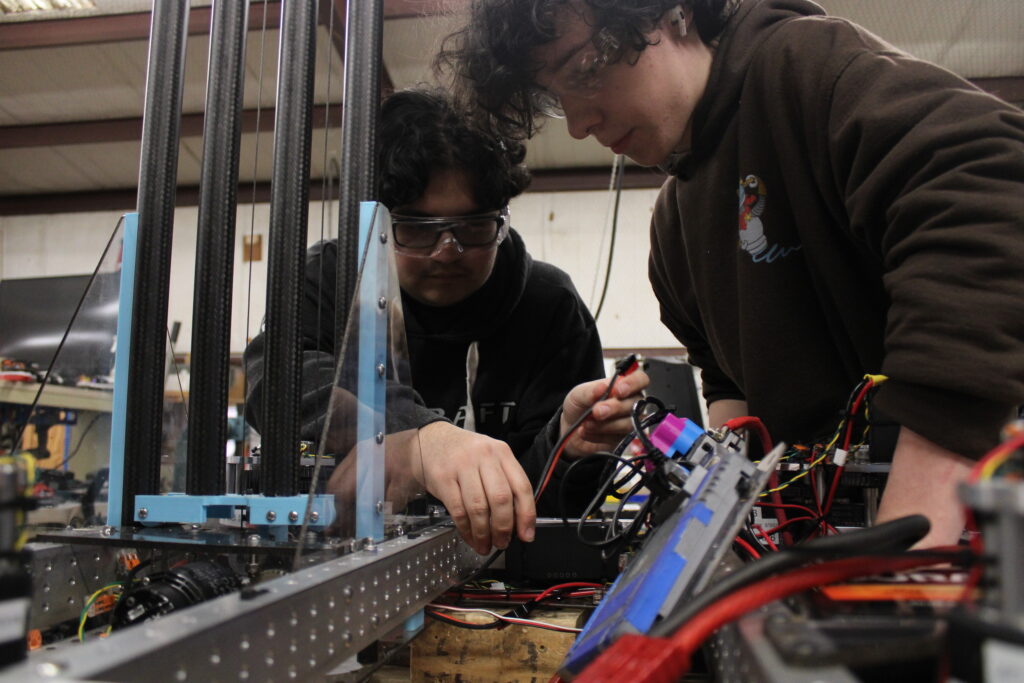
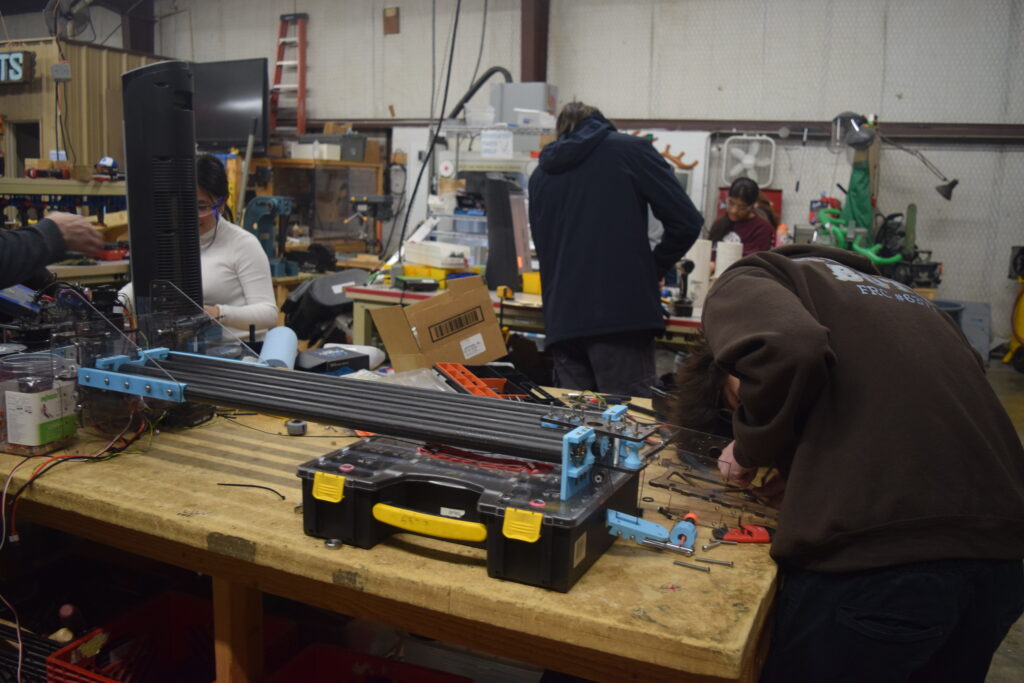
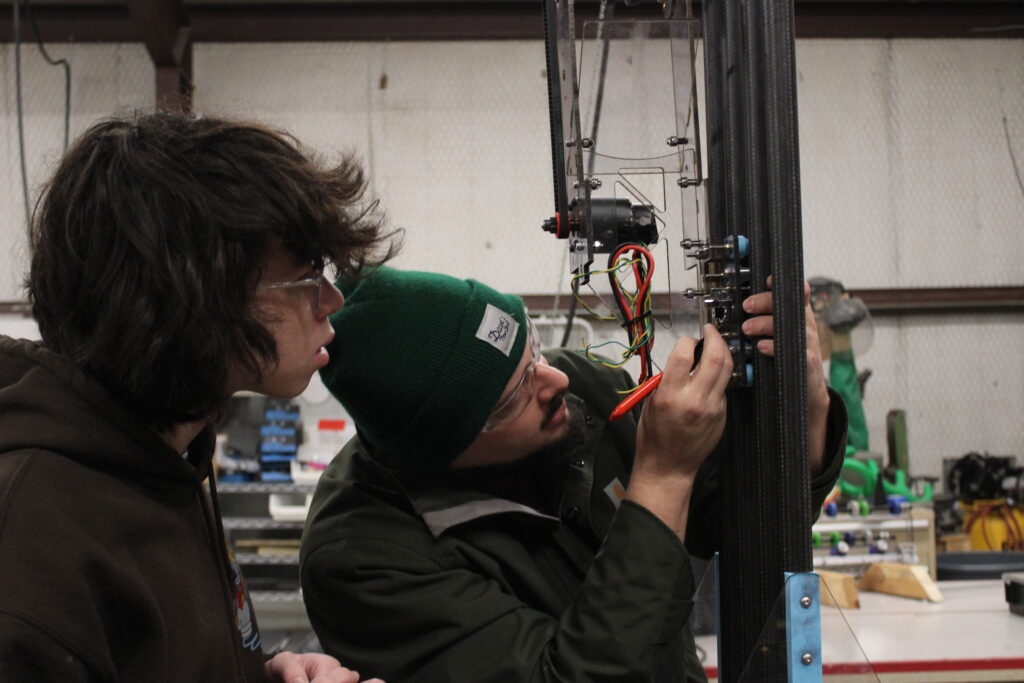
Game Piece Manipulator
The game piece manipulator team has been hard at work, putting the final touches on the CAD design for the sideways translation intake. After testing several prototypes, the team has zeroed in on this one, as it proved to be the most effective and reliable in action. With the CAD completed, our focus shifts to the next phase: cutting and assembling the robot parts. Alongside that, we’ll also be wiring everything up and securely attaching the intake to the competition robot. It’s an exciting time as we move closer to getting the final pieces of the robot ready for the competition!
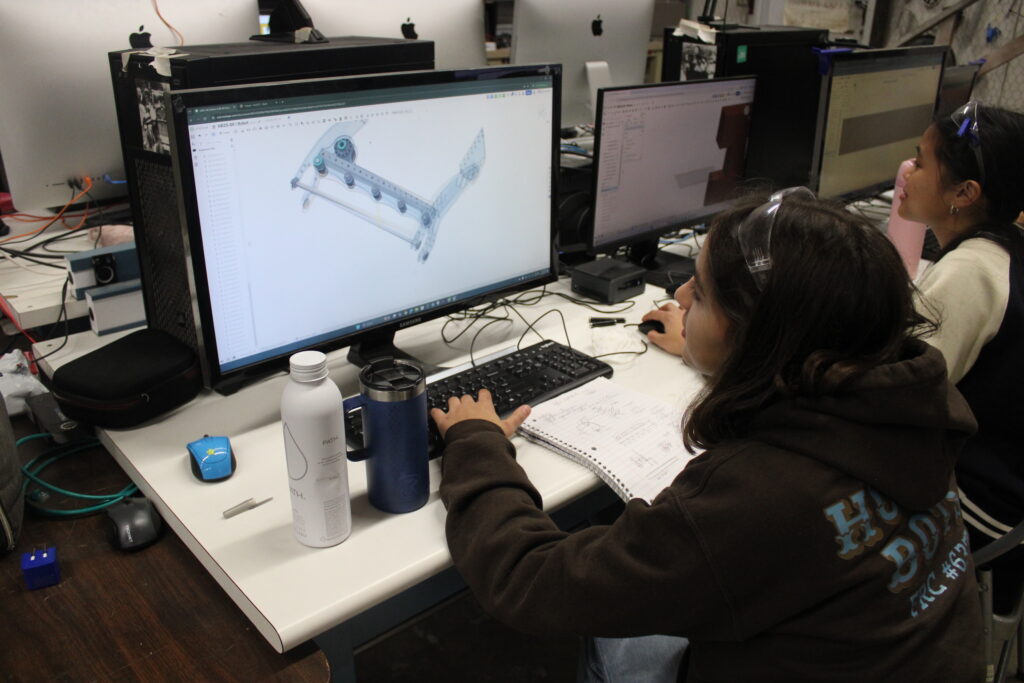
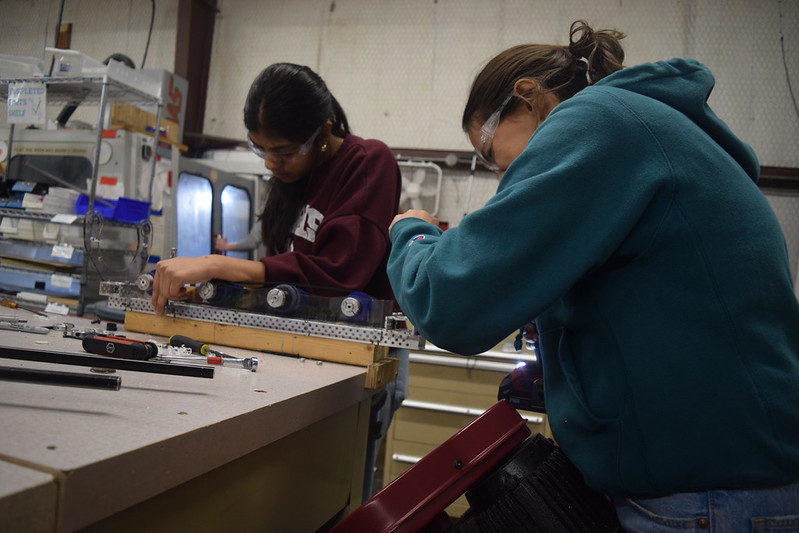
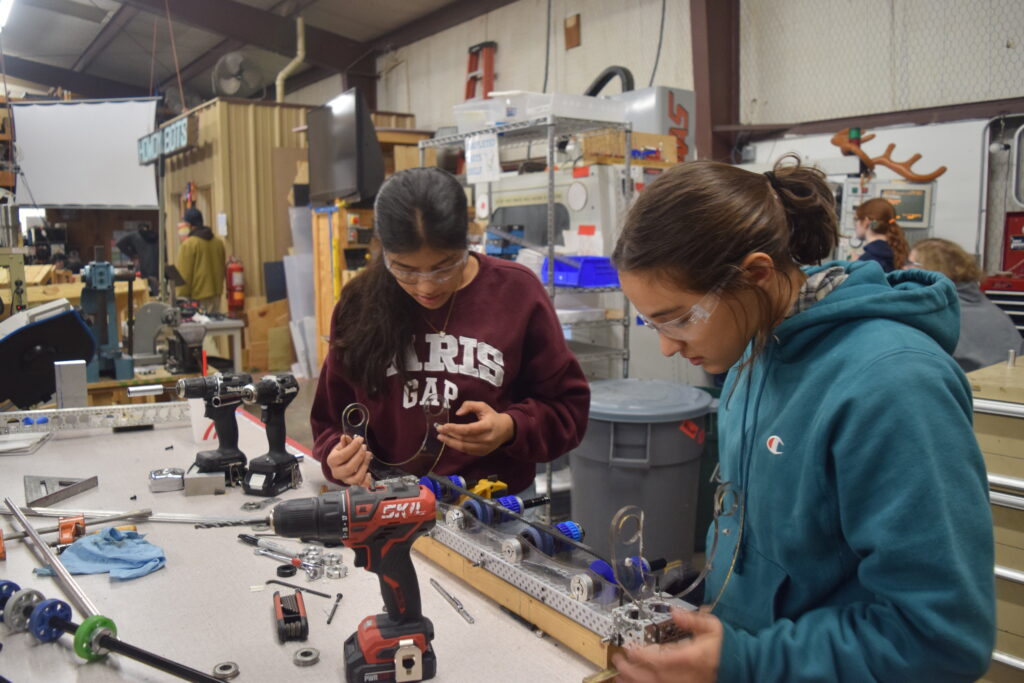
Kitbot Team
The kitbot team has been putting in solid work on crafting a new intake support. However, after drilling the holes, they quickly realized that it was way off from where they needed it and decided to replace the sidebar and disassemble it for further adjustments. After that incident they carefully cut the replacement bar and noted that the CAD should be fully completed before moving forward with making any of the parts. The kitbot teams also designed a brand-new battery holder, repositioning it inside the robot. They did this because the battery had been blocking the algae from being intaked. By making this adjustment, they’ve cleared up a lot more space, allowing the algae intake to operate smoothly as it pulls algae inside the robot to be able to move it to the processor. Along with all of this they have done some wire management moving some electrical stuff around for organization.
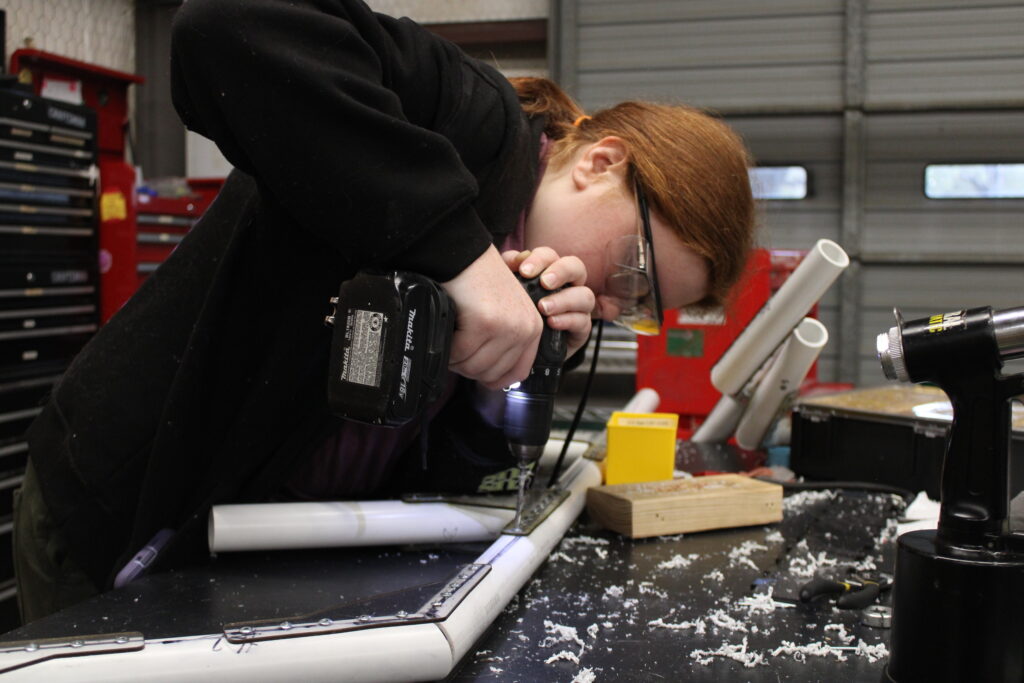
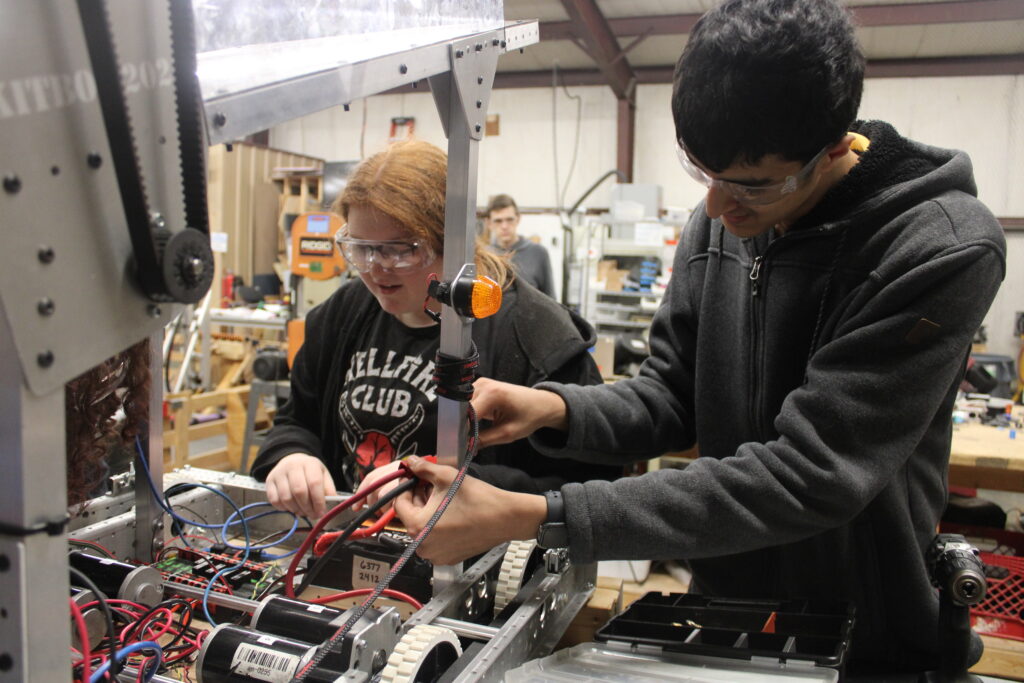
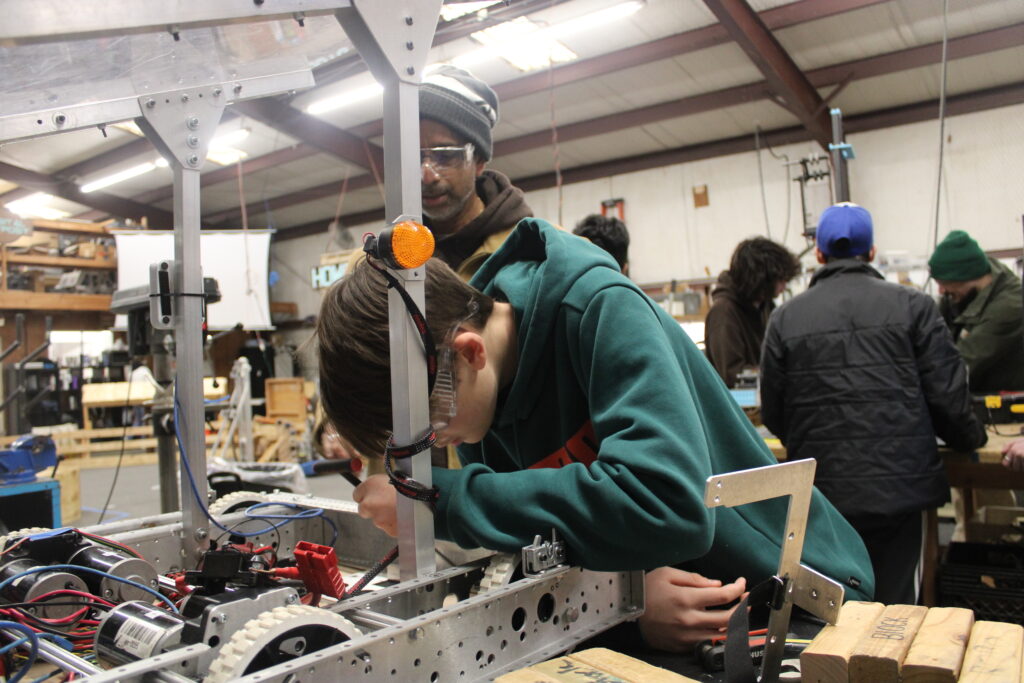
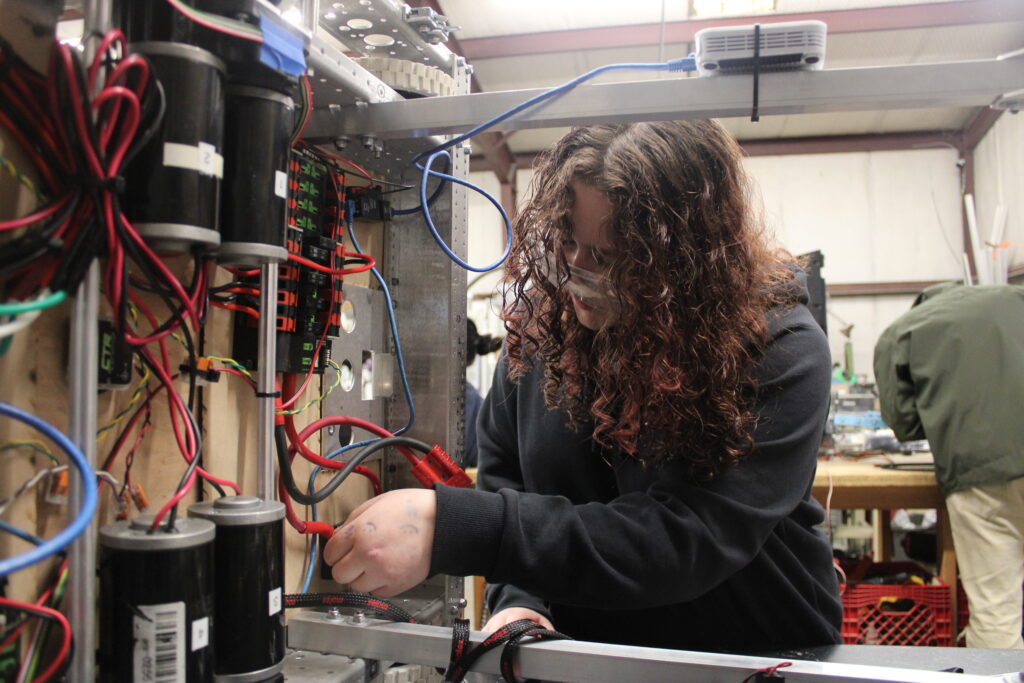
SEE YOU NEXT WEEK!
With the competition robot being tested and parts being iterated/ finalized we cannot wait to see how it will look out on the field competing and working with other teams during competition. We hope you continue with us on this journey and see what we do next!
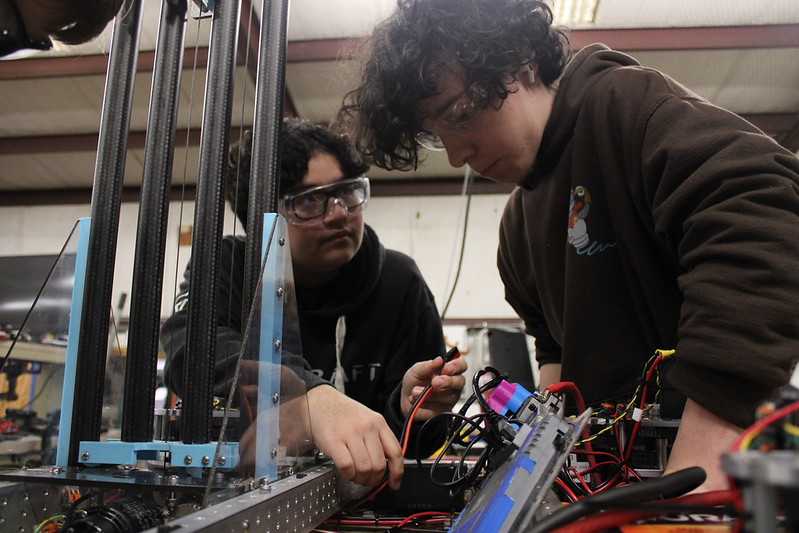
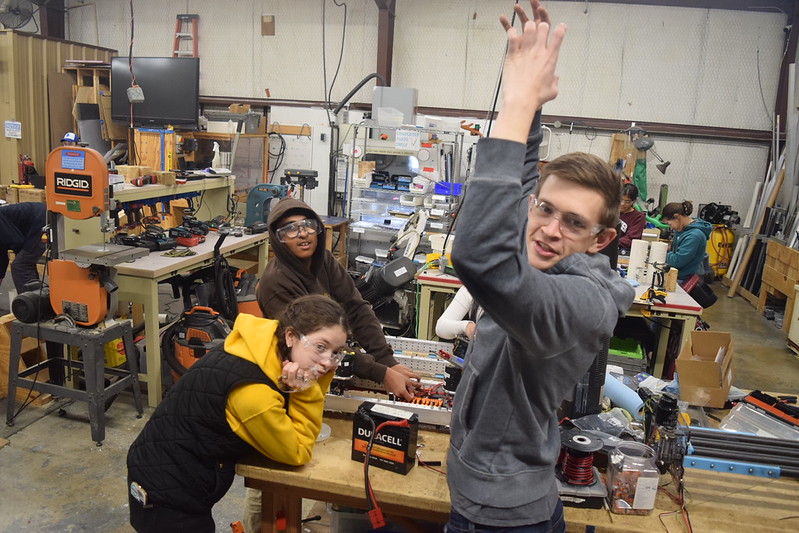
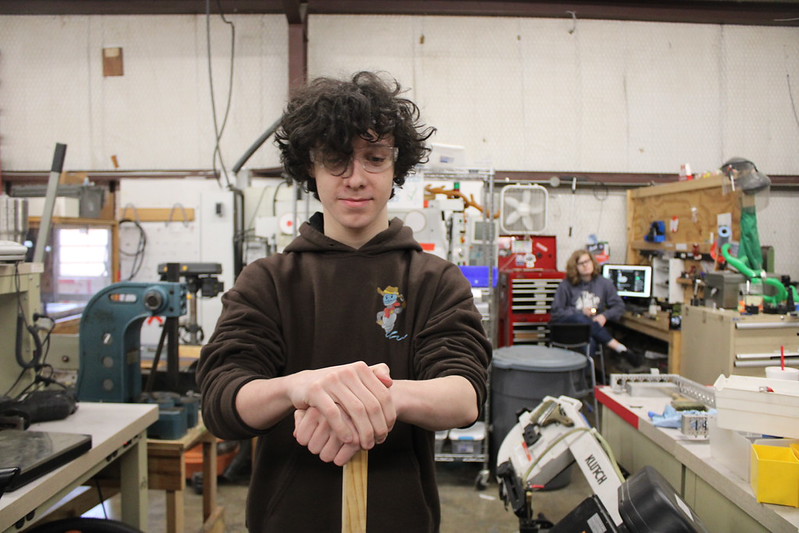
“just be taller so you can do this” – Andrew
Leave a Reply
You must be logged in to post a comment.